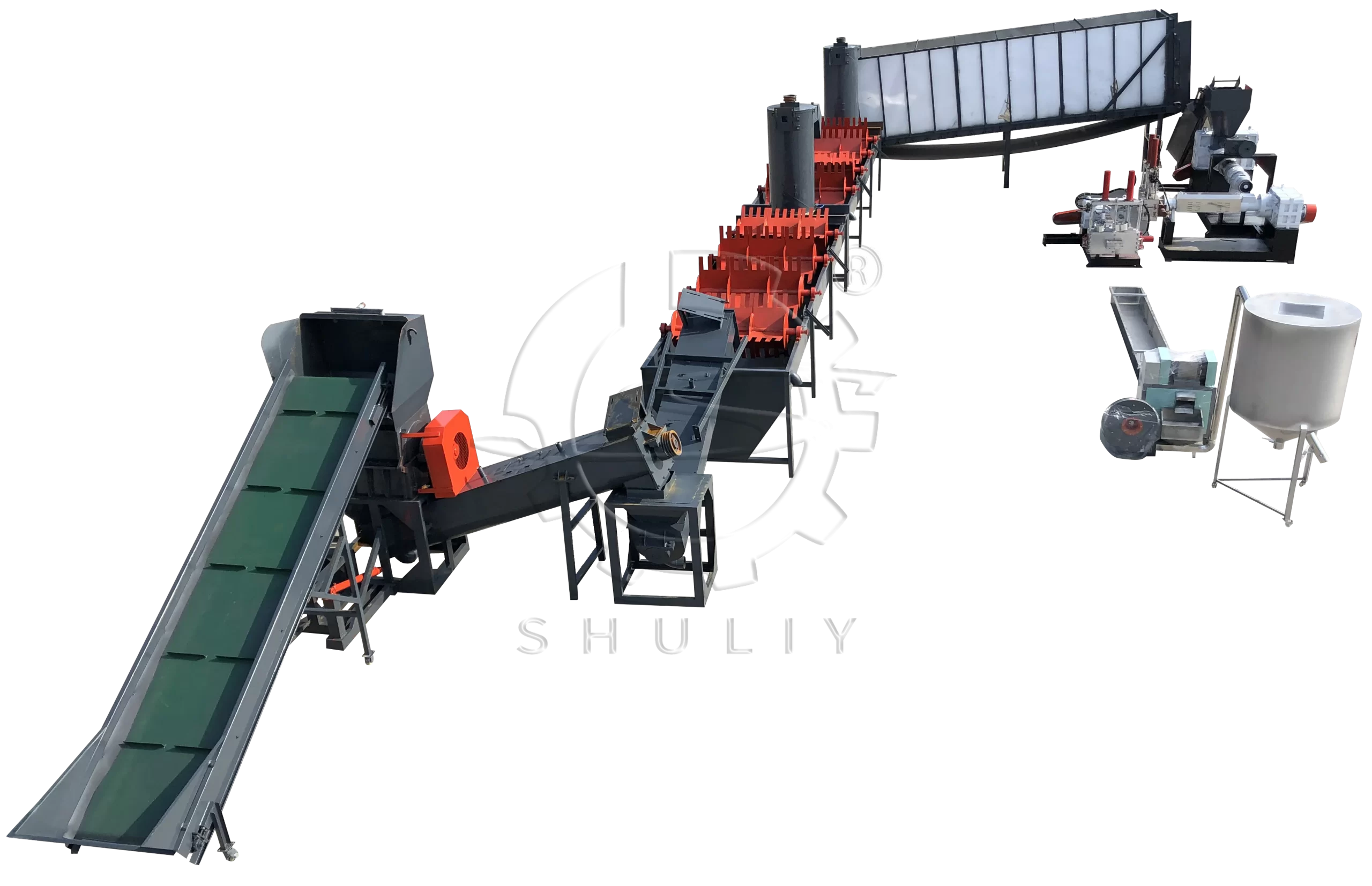
Our PE plastic flake pelletizing lines provide quick and easy plastic pollution solutions for recycling dirty rigid plastics (e.g. HDPE bottles, furniture casings, pipes, etc.). Rigid plastics are cleaned and pelletized using efficient recycling machinery connected by a series of conveyors. The end product is a completely clean plastic granule that can be reused in manufacturing. Our granulation lines have capacities ranging from 100 kg/h to 500 kg/h.
While our standard plastic flake pelletizing lines are sufficient for most facilities, customized setups with additional configurations of machinery and increased throughput can be designed to meet your specific needs.
The following is a detailed description of our equipment and pelletizing process.
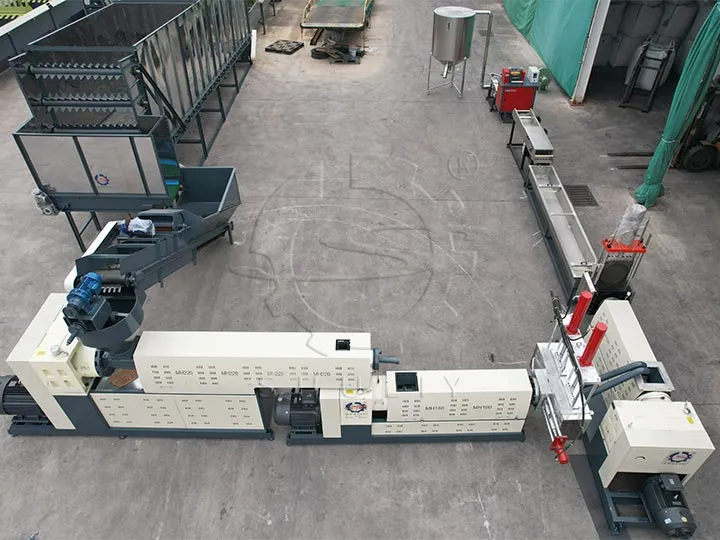
Granulating Line Configuration
Our complete plastic recycling units include processes such as shredding, washing, drying, granulating, cooling, cutting, and storage, forming a fully automated and efficient system.
However, our equipment setup is also highly flexible. For clients who only require specific sections like crushing and washing or just the granulation part, we can customize the system accordingly to meet their exact needs.
This adaptability ensures that customers get a solution tailored to their specific production requirements without unnecessary components. In addition to this, there are many other advantages of our waste recycling machine, so please read on.
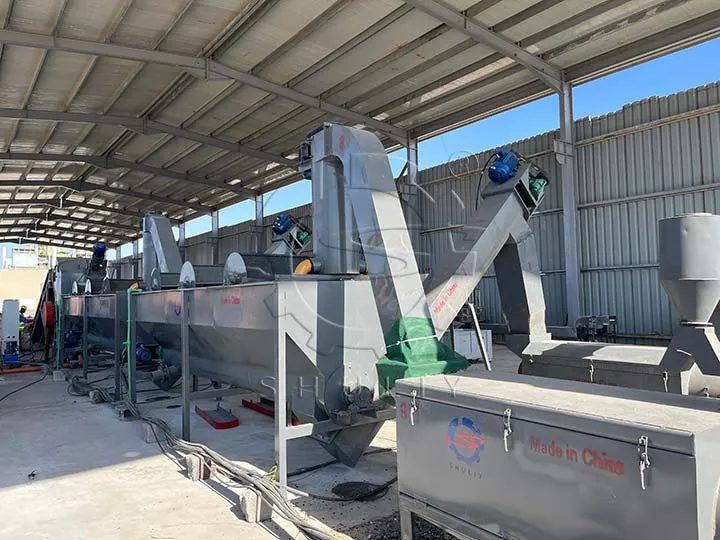
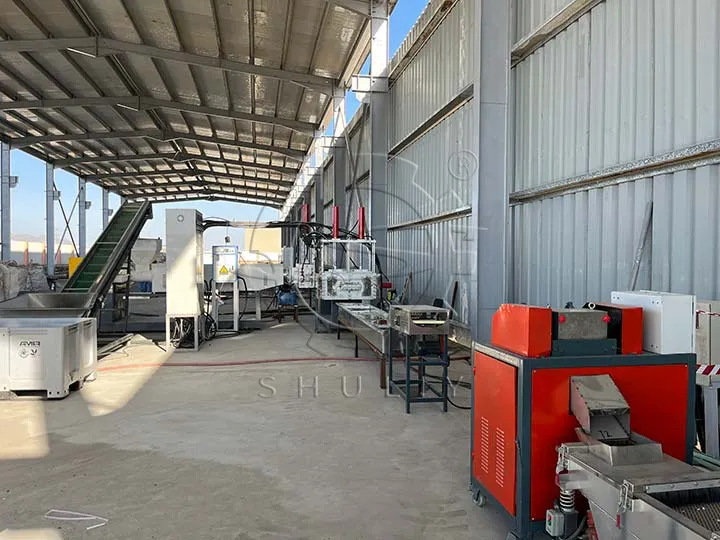
Advantages of Our Waste Recycling Machine
- Capacity: Standard capacity ranges from 100kg/h to 500kg/h, and higher capacities can be customized to meet large-scale production.
- Productivity: The optimized production process significantly reduces downtime and improves overall efficiency.
- Automation: A high level of automation is designed to reduce the need for manual labor.
- Material compatibility: the equipment is compatible with a wide range of hard plastic materials, high flexibility, to adapt to the production needs of different customers.
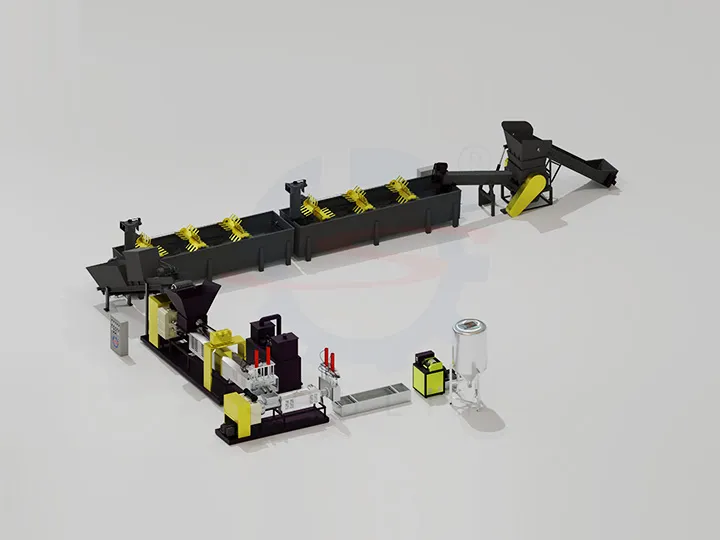
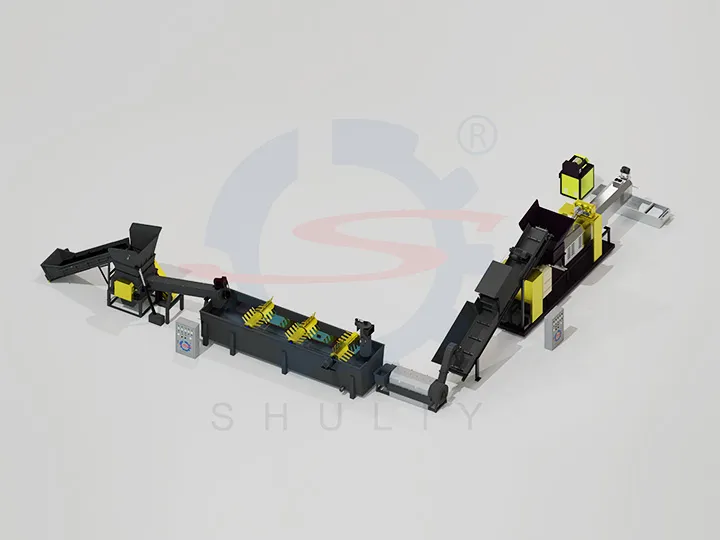
Materials Suitable For Pelletizing
Here are some materials suitable for granulation, but the list is not exhaustive. If you’d like to know whether your material can be granulated or how the process works, feel free to leave your contact details on our website. One of our sales managers will reach out to you soon with more information.
Rigid plastics that can be processed in a plastic recycling line include plastic drums, food containers, injection molded materials or products, plastic basins, plastic pallets, plastic toys, furniture and appliance shells, plastic chairs, and more. The final product is plastic pellets that can be used to make new plastic products.
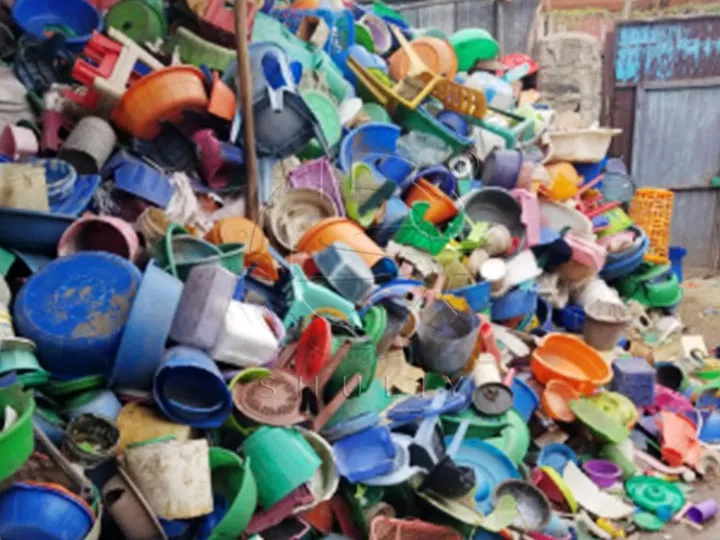
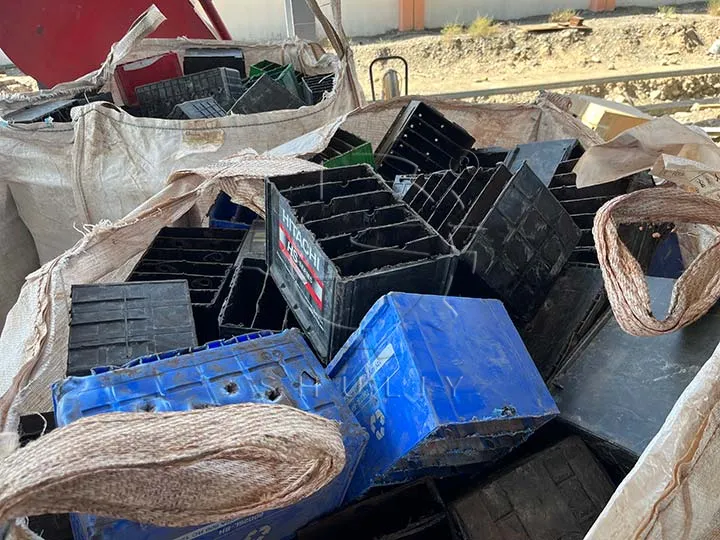
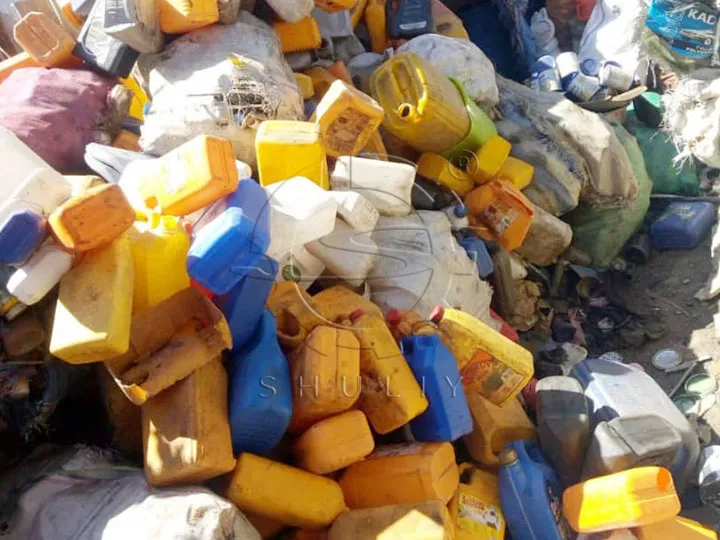
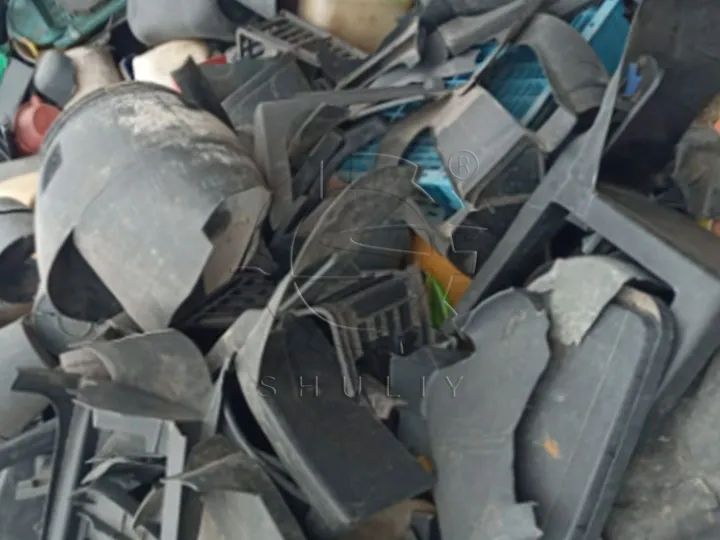
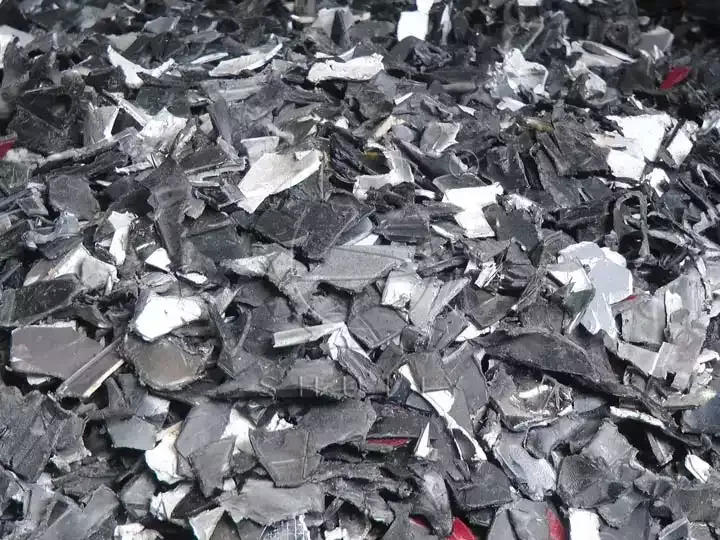
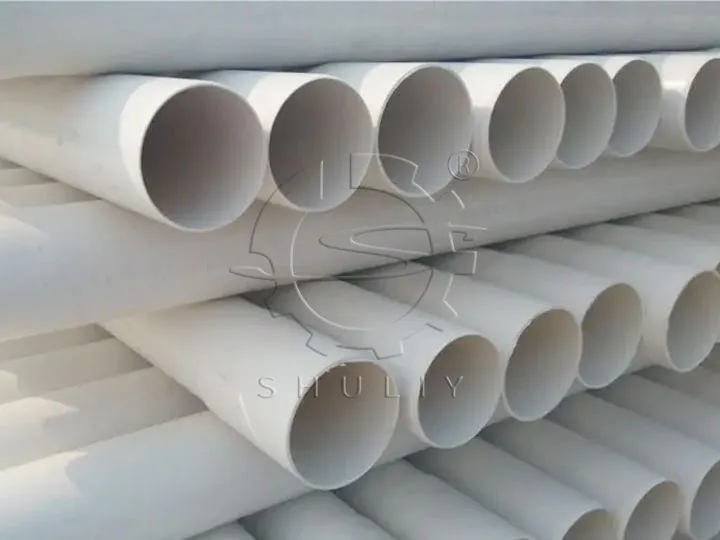
Final Product-Recycled Plastic Pellets
Recycled plastic pellets have a wide range of uses. Extrusion molding can be used for pipes and plastic sheets; injection molding is suitable for the manufacture of high-precision products such as electrical appliance housings and automotive parts; and blow molding is used for the production of plastic bottles or large-volume containers. These processes offer a wide variety of applications for recycled plastics, helping them to play an important role in a variety of fields.
In addition, the color of the recycled plastic granules can be determined by adding color masterbatch or pigments during the melting process of the plastic, enabling customers to produce recycled plastic products that meet the color requirements.
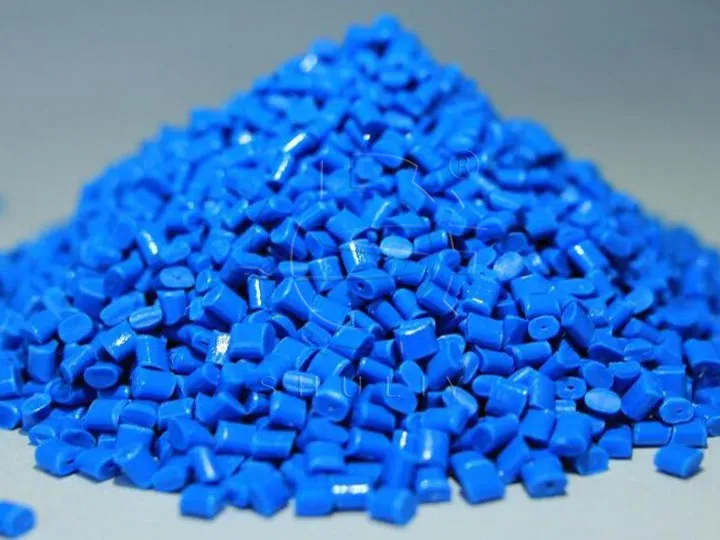
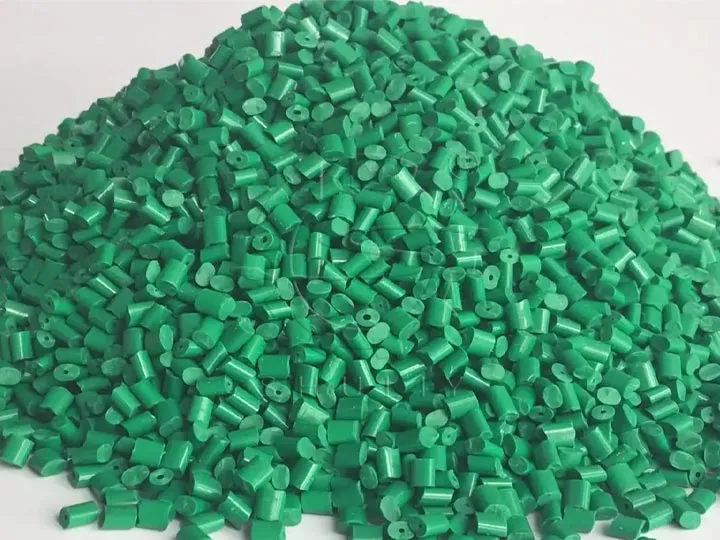
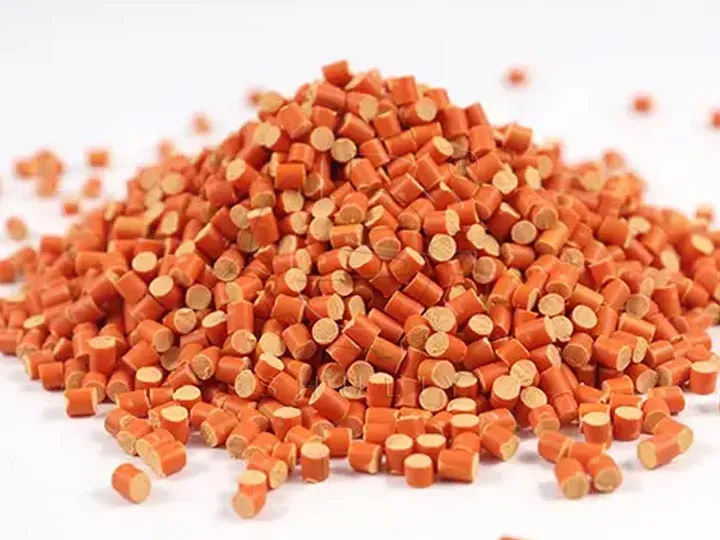
PE Plastic Flake Pelletizing Line Process
NO. | Process | Machine | Description |
1 | Linking the individual machines and conveying the raw materials. | Conveyor belt | This seamless transfer ensures continuous and efficient recovery. |
2 | Crushes plastic into small pieces that are easy to pelletize. | Plastic crushing machine | This step is crucial for subsequent granulation, as large pieces of plastic cannot be put into the pelletizer machine. |
3 | Cleaning of plastic waste after the shredder | Plastic washing machine | Removal of impurities, contaminants, and residual material ensures the high quality of the final plastic pellet. |
4 | Removing water from recycled plastics | Dewatering machine | To prevent adverse effects on the plastic pelletizing process |
5 | Extruding crushed plastic into plastic strips | Plastic granules making machine | Melt and extrude the plastic. The extruder is the heart of the entire recycling process. |
6 | Cool down the extruded plastic strip. | Cooling tank | High-temperature plastic strips cannot be cut and need to be cooled and solidified first. |
7 | Cut cooled plastic strips into uniformly sized plastic pellets. | Granules cutting machine | Homogeneous plastic granules are of good quality and high price. |
PE Plastic Flake Pelletizing Line Main Machine Show
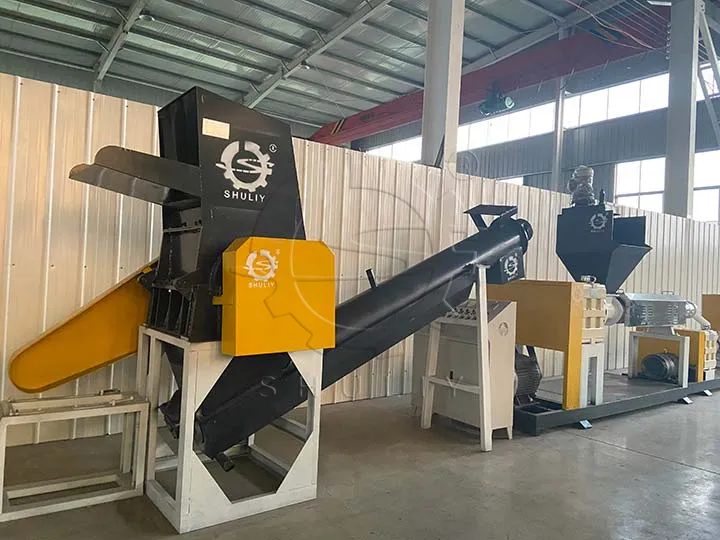
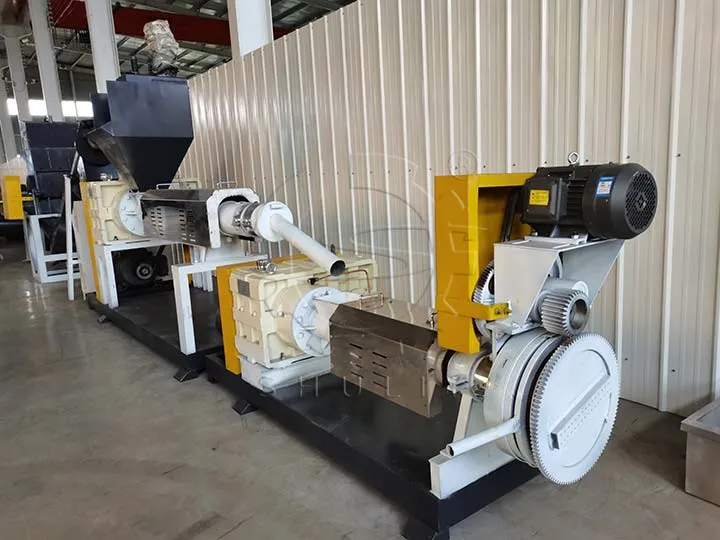
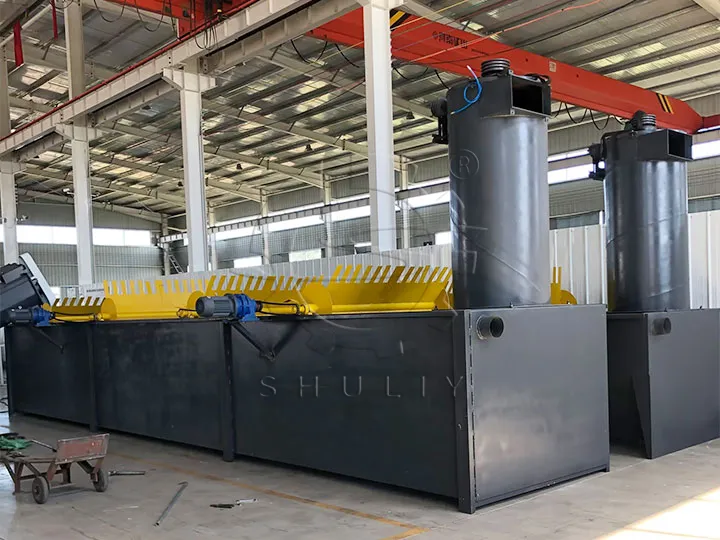
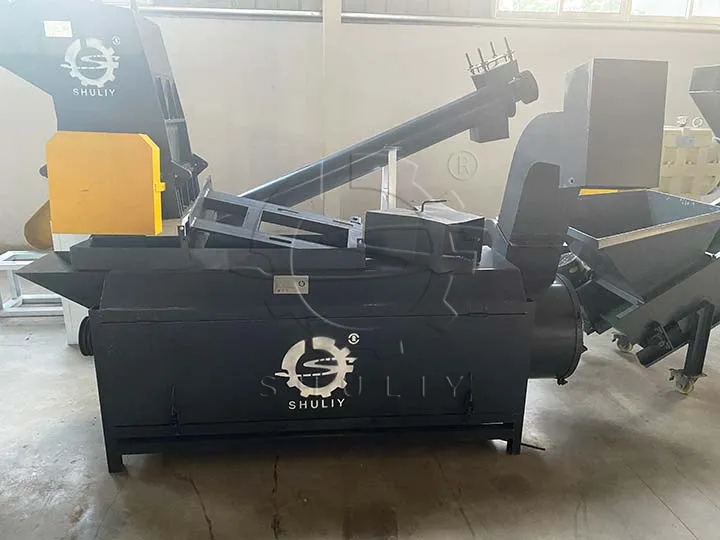
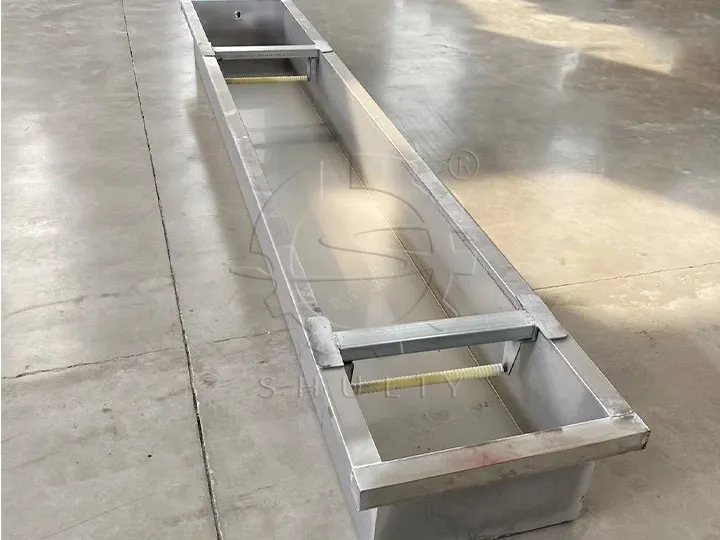
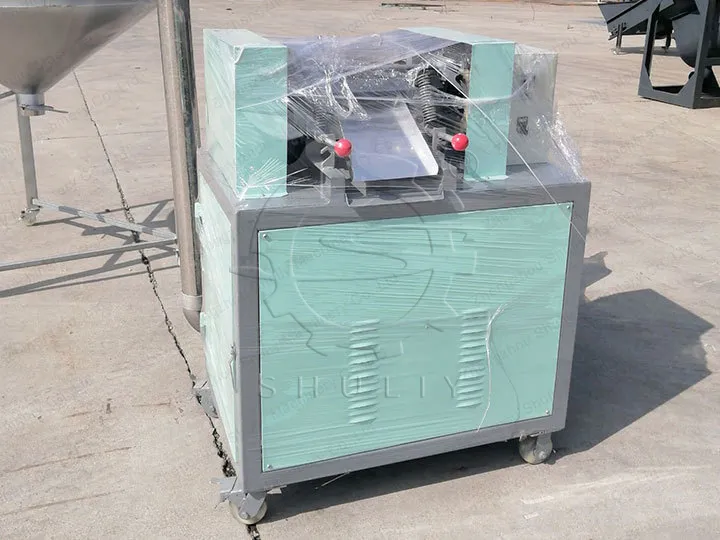
Demonstration of The Entire Pelletizing Process
In the video below, we look at how waste plastic is processed into recycled plastic granules with these plastic recycling machines working together.
Here’s a video of the unit running successfully after our engineers assisted with the installation in Oman, the recycled material is PVC.
Plastic Recycling Machine For Sale
In addition to Oman, we also work with Kenya, Ethiopia, Iran, Tanzania, Togo, Nigeria, Saudi Arabia, Cote d’Ivoire, Ghana, Botswana, Indonesia, Congo, UAE, South Africa, South Sudan, Zambia, Philippines, Zimbabwe, Somalia and many other countries.
These collaborations enable us to gain a deep understanding of the needs of different markets and provide customized solutions for customers in various countries. With years of industry experience and technology accumulation, we can respond quickly to customer requirements and ensure the efficient operation of equipment. Through close cooperation with customers in different countries, we continuously optimize our product design and service processes to meet the special needs of different regions.
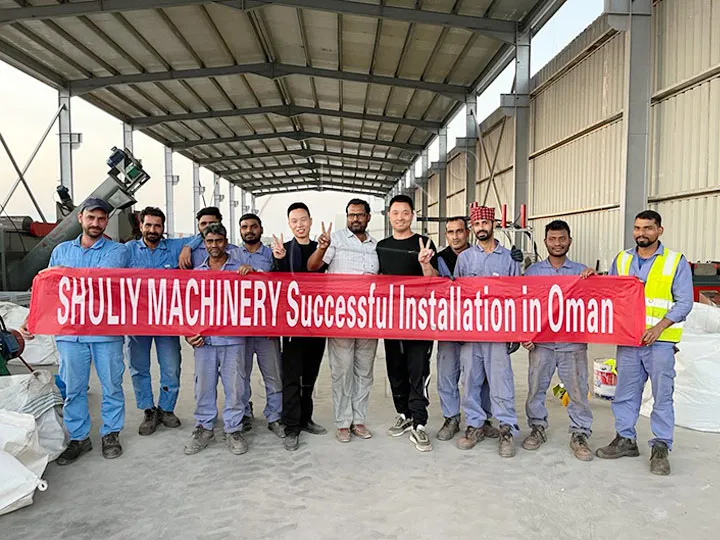
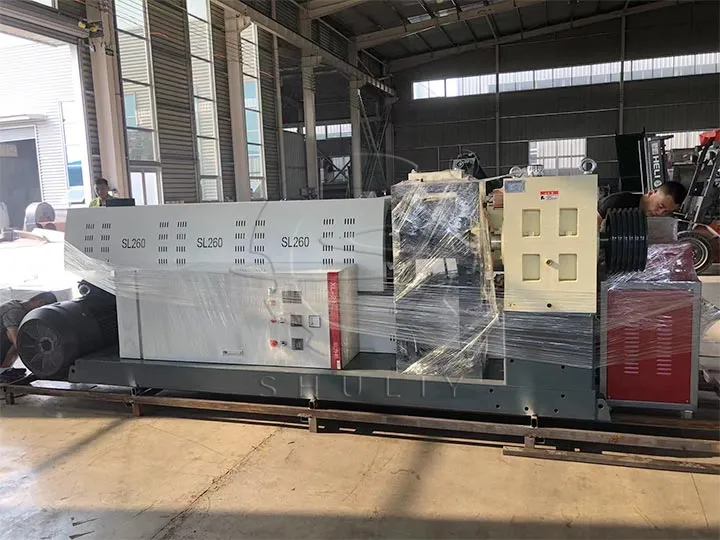
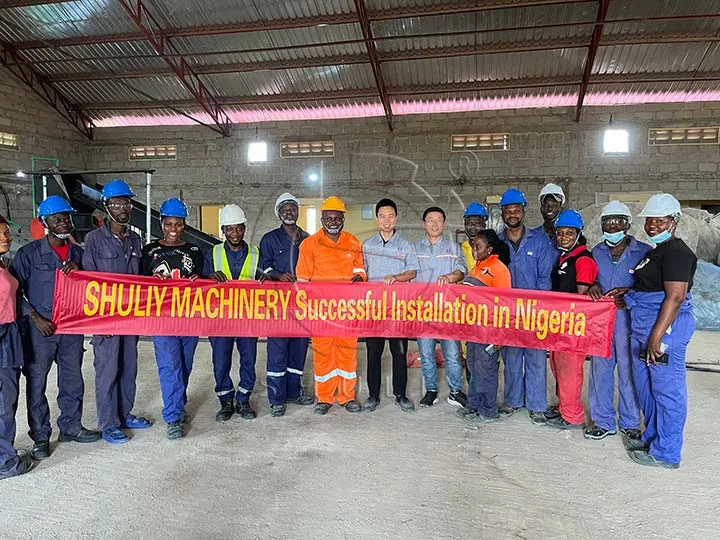
Get Plastic Recycling Granulating Line Price
As a plastic granulating line supplier, we know that price is one of the important factors for customers’ decisions. We offer reasonably priced pelletizing lines, taking into account the performance of the equipment, the advancement of the process, and the guarantee of after-sales service. Through flexible configuration and optimized design, we ensure that our customers get the best price/performance ratio while meeting their production needs.