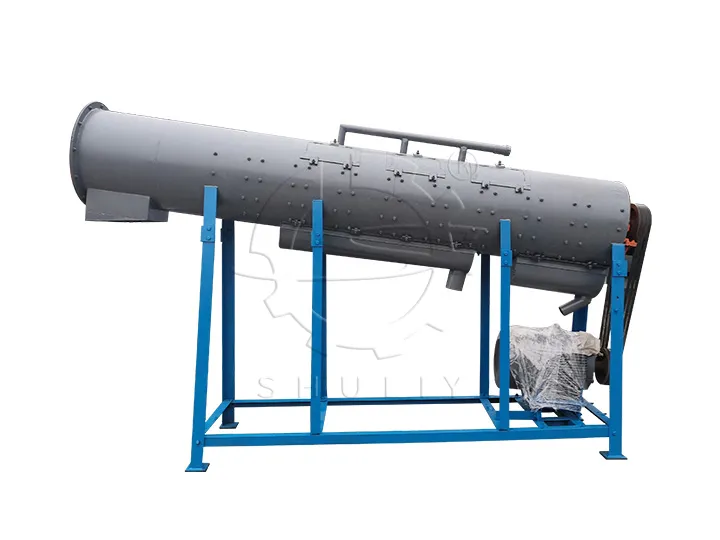
The friction washer is a kind of efficient equipment specially designed for cleaning PET bottle flakes, which is commonly used in PET bottle recycling lines.
It carries out strong friction and rinsing on PET bottle flakes through the high-speed rotating spiral shaft and brush device, assisted by water flow, effectively removing dirt, grease, glue residue, and cleaning powder on the surface of bottle flakes.
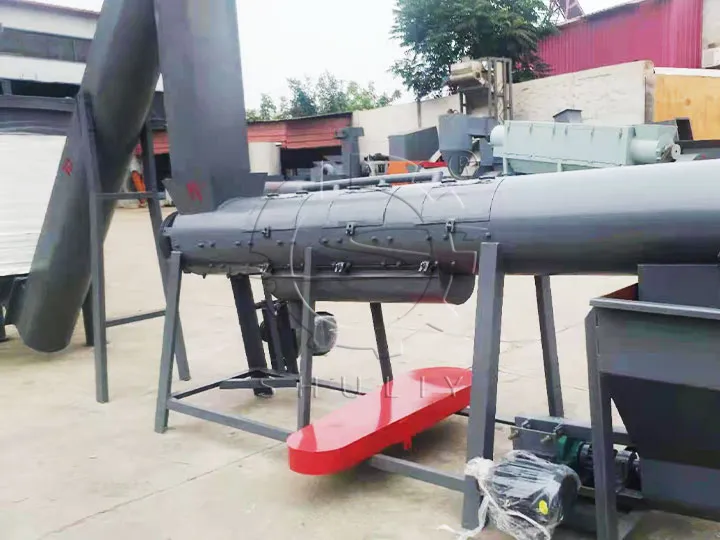
Features of friction washing machine
- Inclined Design: Typically designed with an inclined angle to facilitate drainage and improve washing efficiency.
- Efficient Cleaning Structure: Equipped with multiple paddles and scrubbing strips inside to enhance the friction cleaning of PET bottle flakes.
- High Flexibility: The position can be adjusted flexibly to suit different factory layouts and production needs.
- Customizable: When purchased individually, the height, feeding size, and other specifications can be customized to integrate seamlessly into existing production lines.
How Does Friction Washer Work?
PET flakes friction washer through the high-speed rotation of the spiral shaft and the design of the rubbing plate and rubbing strips, under the action of the water flow to achieve strong friction on the surface of the bottle flakes and rinsing.
This physical friction combined with water flushing can not only effectively remove stains, but also clean off the residual label paper and glue particles in the bottle flakes, to ensure that the cleanliness of the cleaned bottle flakes meets the requirements.
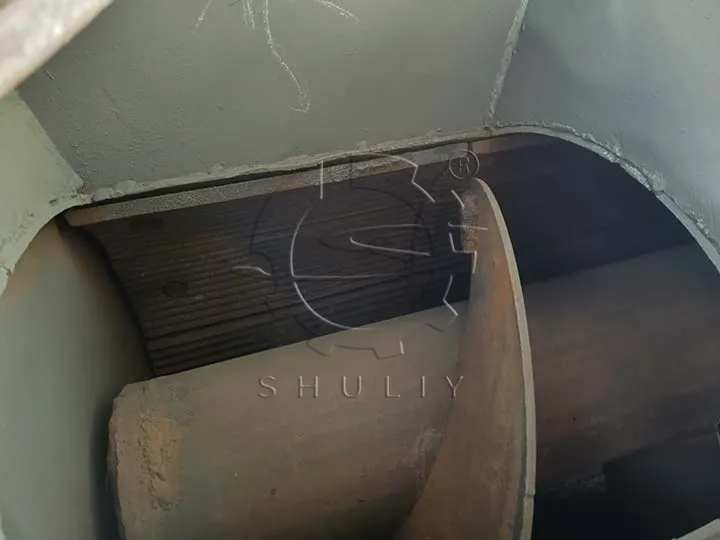
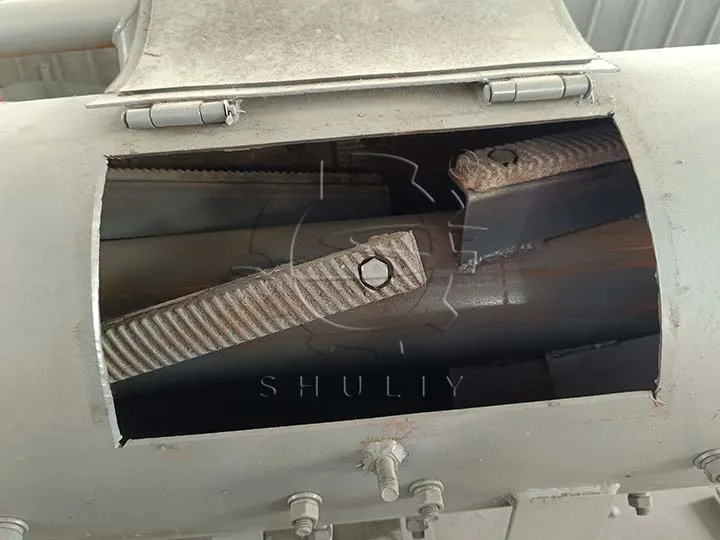
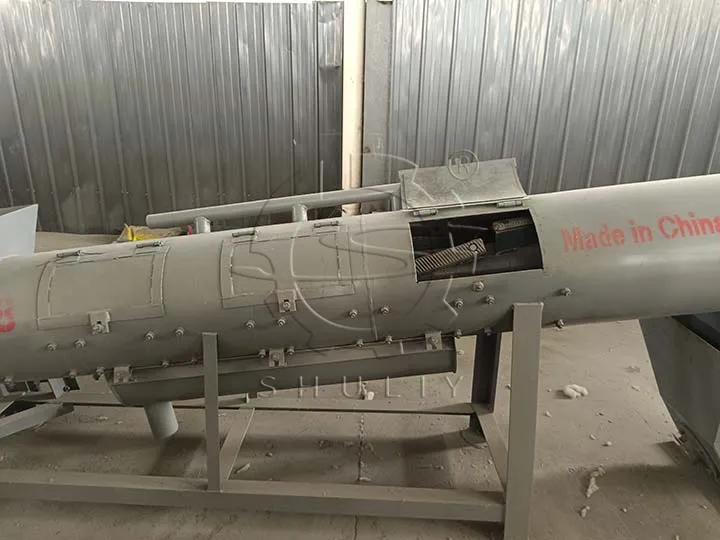
The Role of Friction Washing Machines
In a plastic bottle recycling line, the friction washing machine plays a crucial role in ensuring that the PET bottle flakes are thoroughly cleaned before further processing. Typically, a single friction washing machine is used, but for higher production volumes and stricter product quality requirements, two machines can be installed.
- First Friction Washing Machine: Installed after the separation tank, the first washing machine is responsible for the initial cleaning of PET bottle flakes. It helps to remove impurities such as dirt and labels, ensuring the material is ready for further processing.
- Second Friction Washer: For enhanced cleanliness, a second friction washing machine is often installed after the hot wash tank. This machine effectively scrubs away any remaining cleaning powder or detergent residue from the hot wash tank, further reducing the pH value and ensuring the quality of the washed PET flakes.
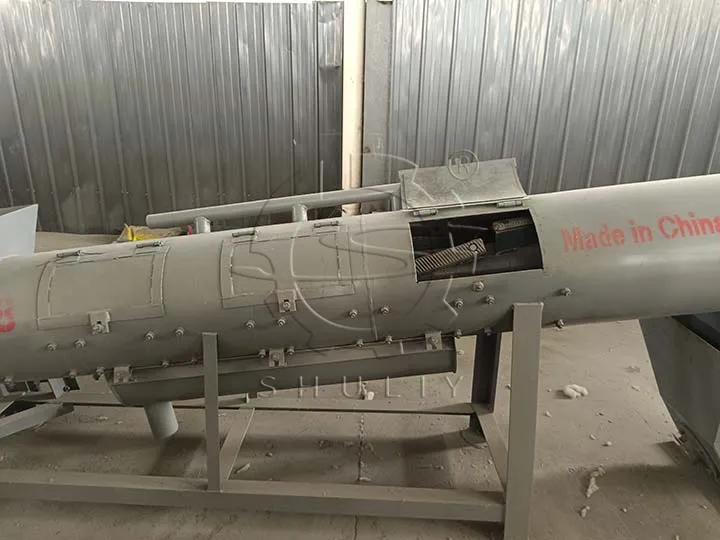
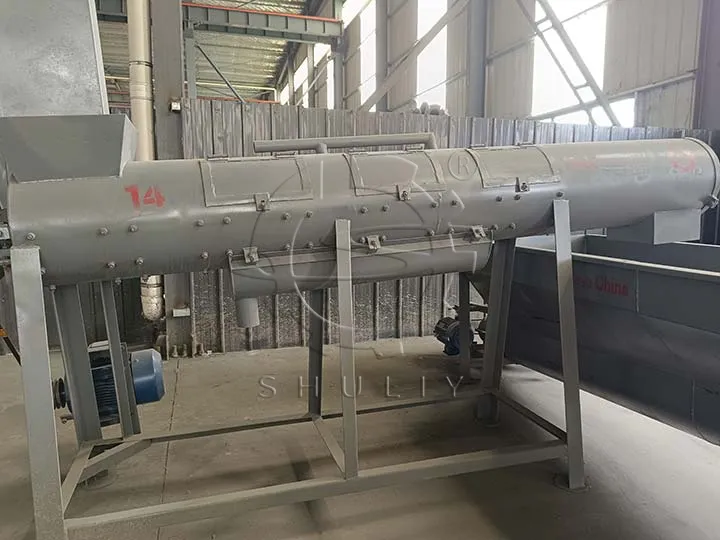
Friction washer Data
Model | SL-1000 |
Capacity | 500-1000kg/h |
Length | 3000mm |
Power | 7.5kw |
Out Layer | 4mm |
Customized Friction Washing Machine For A Nigerian Customer
We customized a friction washing machinefor our Nigerian customer so that it would fit perfectly into the customer’s existing plastic bottle washing line. We customized the height of the feed and discharge ports to suit the customer’s existing equipment. The customer also had special requirements for the color and appearance of the machine, which we strictly adopted.
More details can be viewed: How We Designed A Friction Washer Machine For A Nigerian Client?
Washing systems for bottle recycling lines
Hot water washing tanks, friction washers, and plastic flakes washing machines together make up the cleaning system of a bottle recycling line. The number of these cleaning machines can be adjusted appropriately according to the degree of dirtiness of your raw materials. About the bottle recycling line if you have other questions, welcome to leave us a message on the website.
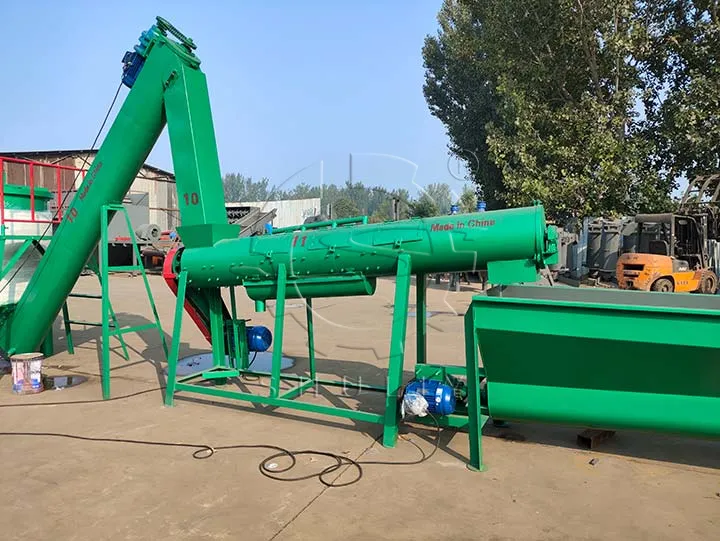