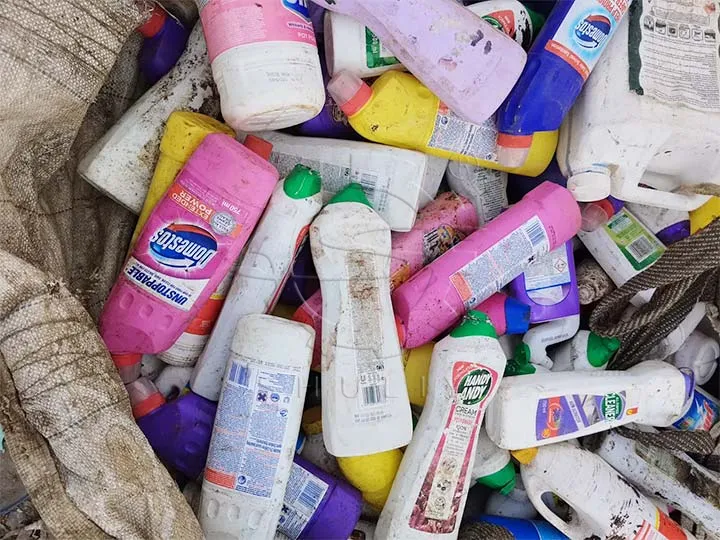
Industrial pelletizer machine is an environmentally friendly machine. When processing waste plastics in an industrial pelletizer machine, different types of plastics show different color variations. These changes are affected by a number of factors, including the type of raw material, the number of times it is recycled, and the processing conditions.
Polyvinyl chloride
After one regeneration, PVC plastic shows a light brown color. After three times of regeneration, it becomes an almost opaque brown color. This change is mainly due to oxidation and degradation reactions caused by high-temperature processing. It should be noted that both hard and soft PVC should be regenerated with stabilizers to maintain color stability.
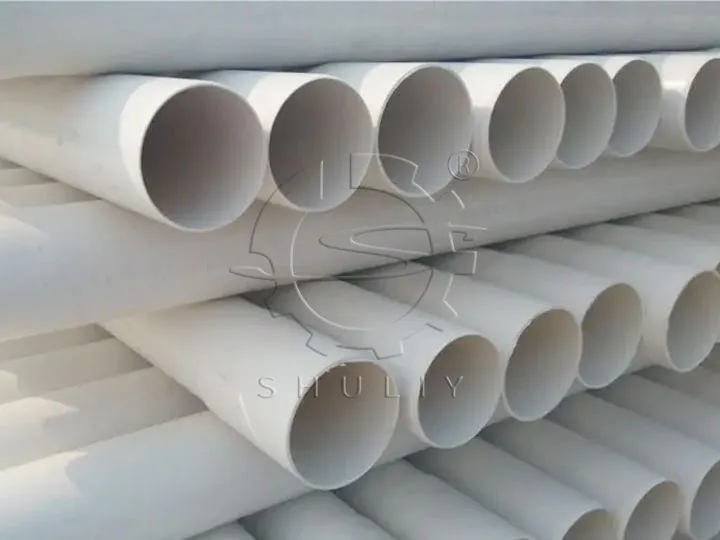
polyethylene
Polyethylene decreases in functionality after regeneration and turns yellow in color. This may be due to high temperatures and chemical reactions during the regeneration process. While the viscosity of high-density polyethylene decreases after multiple extrusion. While low-density polyethylene shows an increasing trend.
polypropylene
After one regeneration of polypropylene, the color remains almost the same, but the melt index rises. After two or more regenerations, the color worsens, but the melt index still rises. Although there is a slight decrease in breaking strength and elongation after regeneration. However, there are usually no significant problems in practical use.
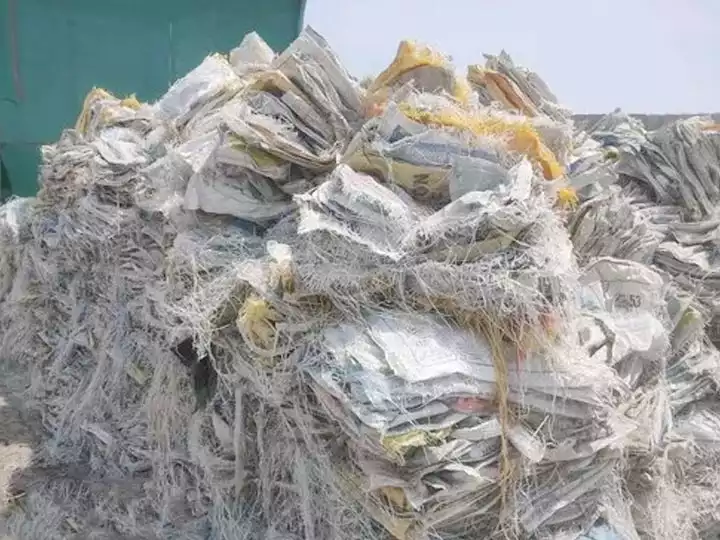
Polystyrene
Recycled polystyrene has a yellow coloration, which usually requires coloring to compensate. The functional degradation of recycled material is directly proportional to the number of times it is recycled.
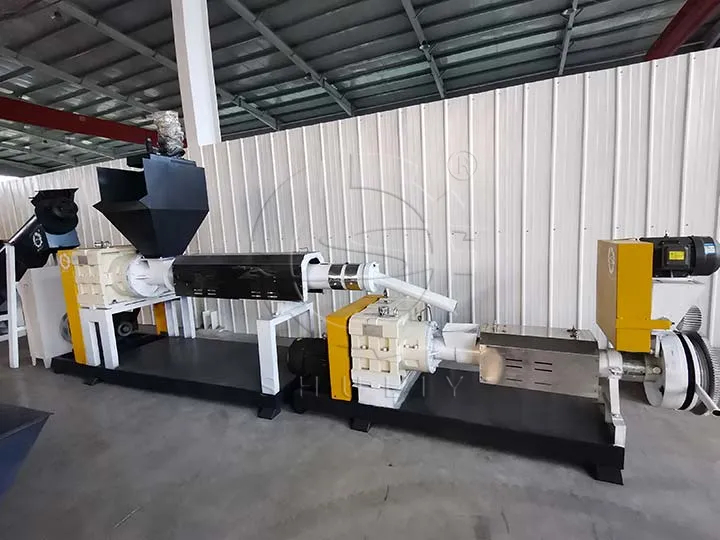
Overall, different plastics exhibit specific color trends after being melted in an industrial pelletizer machine. Understanding these changes can help in adopting appropriate treatment methods during the recycling process to ensure the quality and performance of the recycled plastics.