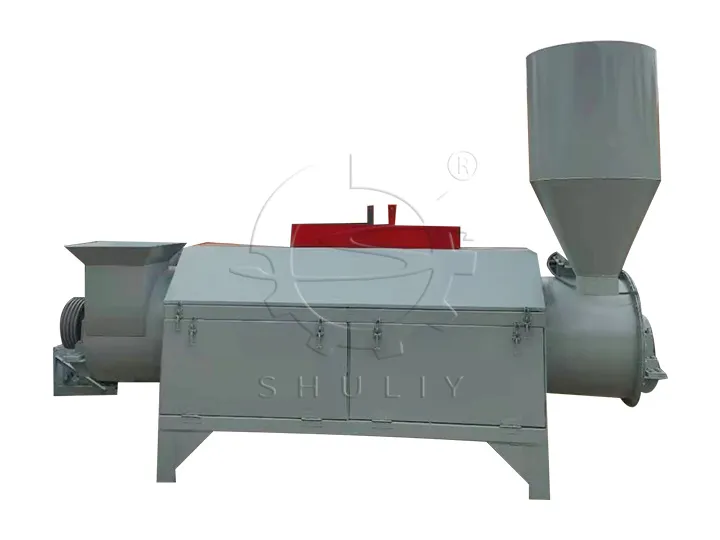
The plastic dryer machine is an important piece of equipment designed specifically for the plastic recycling process and is widely used in the dewatering and drying process of cleaned plastics. Whether it is film, bottle flakes, or hard plastic chips, it can reduce the moisture content of the material through an efficient workflow and provide high-quality drying results for subsequent processing.
Strengths of Plastic Chips Dryer Machine
- Efficient Drying: Remove 95%-98% of the moisture from cleaned plastics, significantly improving drying efficiency.
- Precise Control: Can be equipped with drying pipelines, ensuring the final moisture content is controlled between 0.5%-1%, meeting various process requirements.
- Variety of Models: Offers multiple models, matching the most suitable equipment based on customer production needs.
- Customizable: The equipment can be customized according to customer specifications, including size, materials, and functional optimization.
- Wide Application: Suitable for a variety of plastics, including PET flakes, rigid plastic sheets, film scraps, and more.
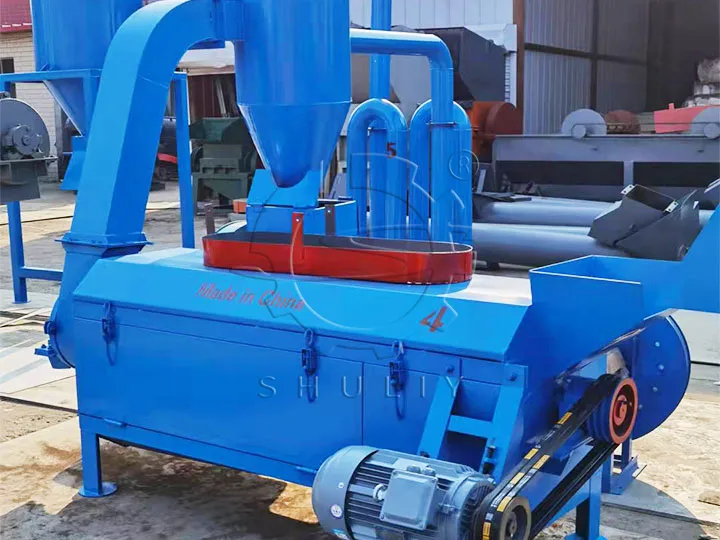
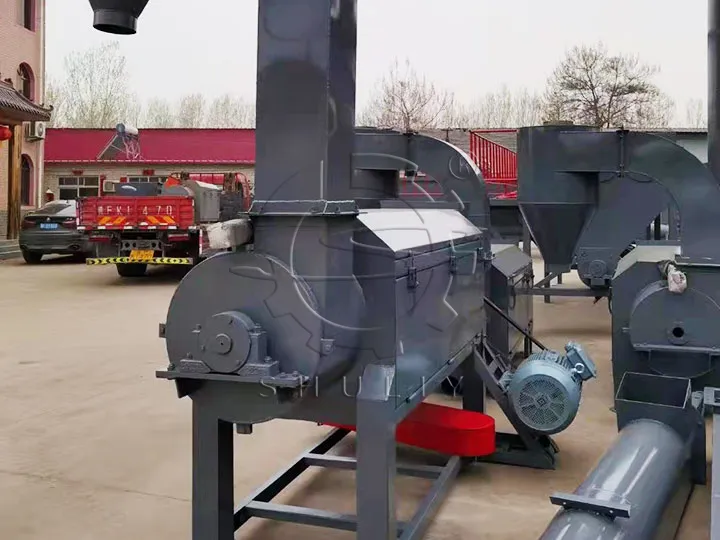
Drying Pipes
For customers with strict requirements on the final moisture content, we offer the option to add drying pipes after the plastic dryer machine. These pipelines help ensure precise control over the moisture level, keeping it within the desired range.
The part of the drying pipe that comes in contact with the material is made of high-quality 304 stainless steel, ensuring durability and resistance to corrosion. This feature enhances the overall efficiency of the drying process and ensures long-lasting performance.
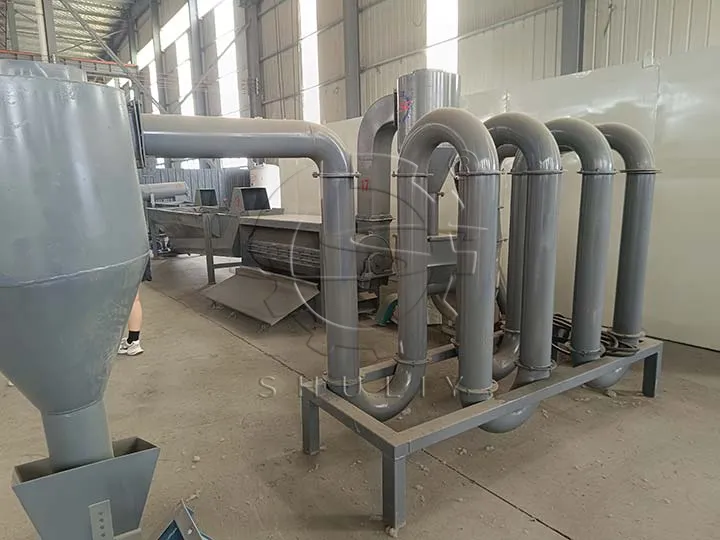
Working Principle of Plastic Dryer Machine
Plastic dryer machines work on the principle of dewatering using centrifugal force. The material is fed into a horizontally placed drum or basket inside the dryer and during the high-speed rotation, the centrifugal force throws the moisture out of the material, which is discharged through the holes on the surface of the drum, while the material continues to be sent to the next step.
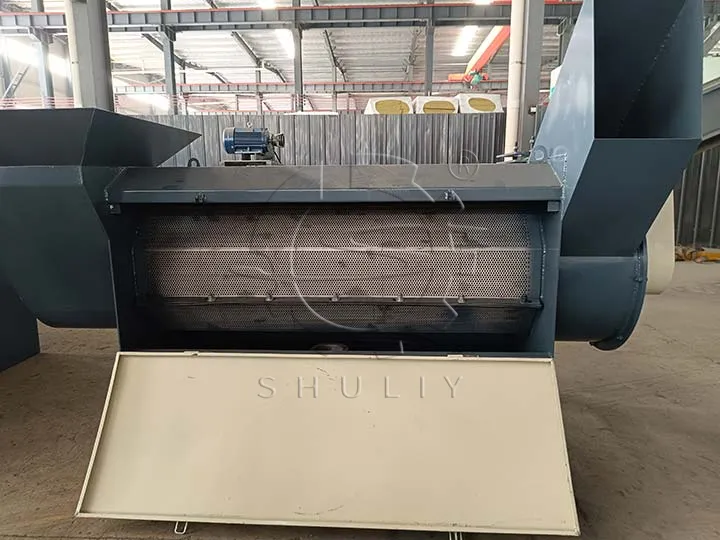
working Video
What Are The Applications of Plastic Dryer Machines?
Plastic chip dryer machines are versatile machines designed to dry various types of plastics, including PET flakes, rigid plastic sheets, and plastic film scraps. They are widely used in recycling plants to remove moisture from cleaned plastic materials before further processing, ensuring the quality and efficiency of the final products.
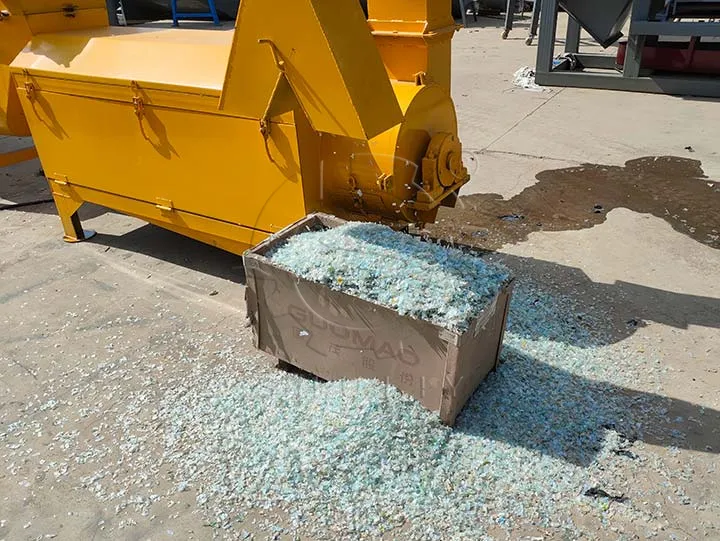
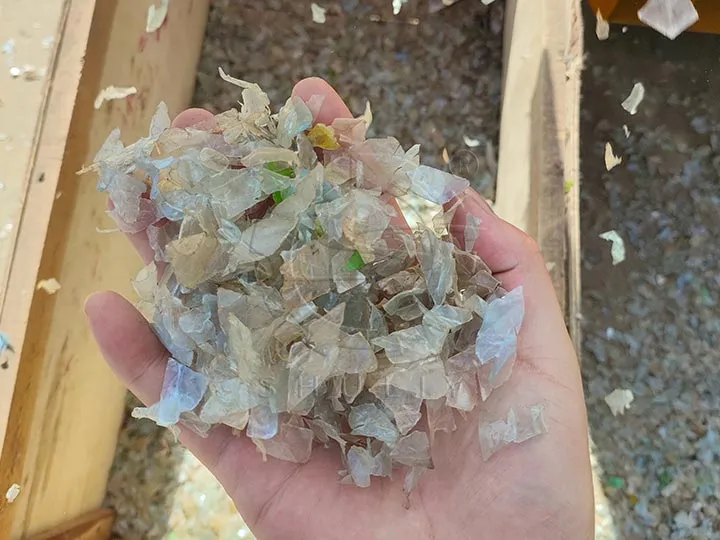
Parameters of Plastic Dewatering Machine
Drying rate | 95%-98% |
Drying pipes | Drying rate: 0.5%-1% Material: 304 stainless steel |
Applicable materials | PET bottle flakes, rigid plastic flakes, film scraps |
Processing capacity | 1000kg/h |
Power | 15kw |
Customisability | Support for customization |
Shuliy also offers a variety of other models and sizes of plastic dryer machines, which can be customized according to specific customer needs. These dryers are designed to meet different production capacities and material types, ensuring optimal performance in various applications. If you’re interested, feel free to contact us for more details and personalized solutions.
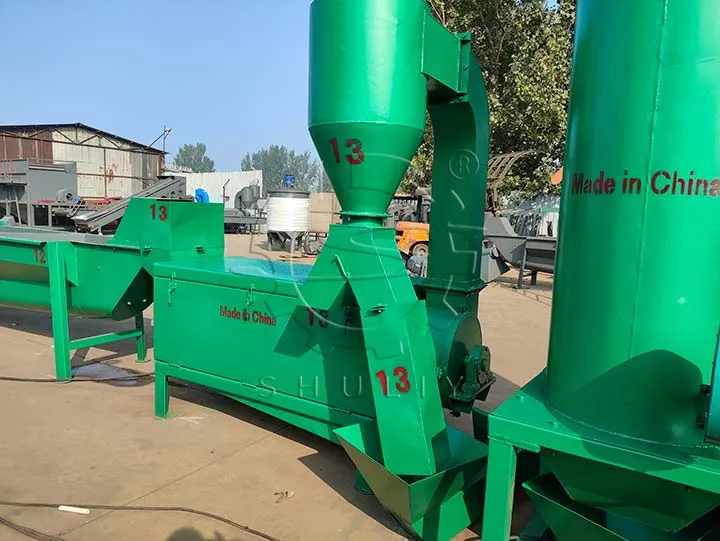
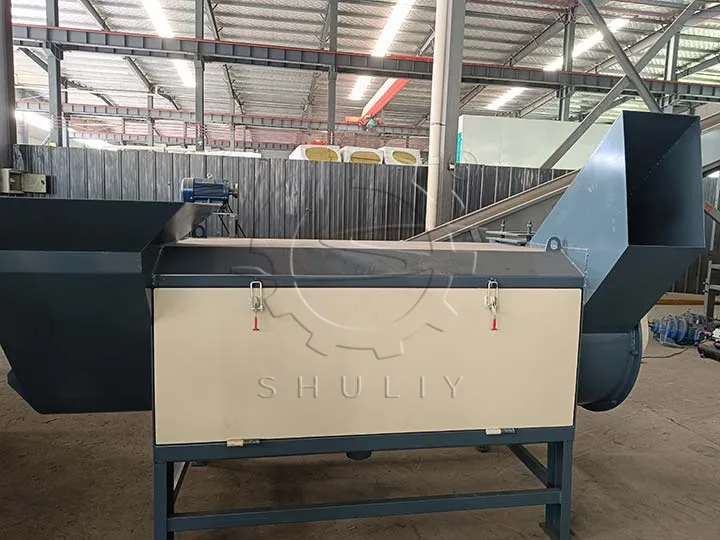
Why Dewatering Is Needed Before Pelletizing Plastics?
Prevent equipment damage: Excessive moisture may cause plastic pellets to bind, increasing the load on the equipment and even damaging the granulation machine.
Improve product quality: residual moisture can affect the granulation process, producing air bubbles or uneven particles and reducing the quality of the final product.
Improve production efficiency: By dewatering, steam generation during the granulation process can be reduced, reducing energy consumption and improving production efficiency.
Prevent contamination: High moisture content may affect the stability of the subsequent process, leading to contamination or poor processing.