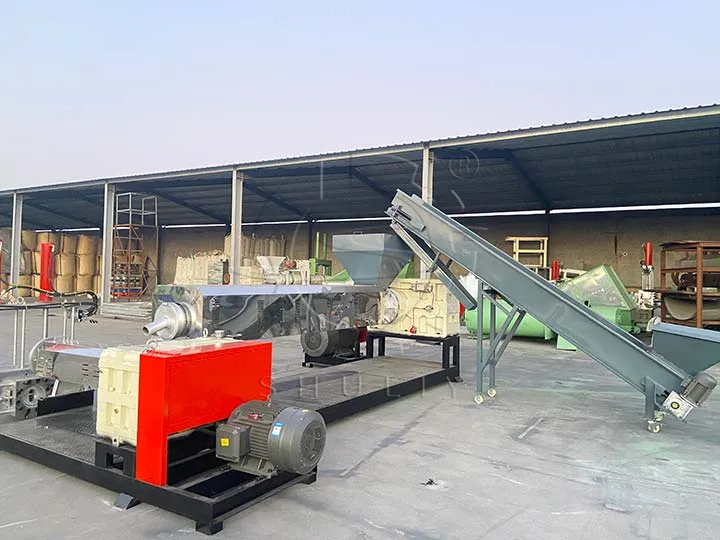
There are four different types of cutting when pelletizing waste plastic pellet making machines. This blog introduces them to you.
Dry cutting
Dry cutting of pellets means that the extruded strip material in the waste plastic pellet making machine is immediately cut into pellets of uniform length by the rotating blades. Then the pellets are sent by the fan through the pipe to the cooling and sieving device.
This type of pelletizing is suitable for the mixing and pelletizing of polyethylene materials.
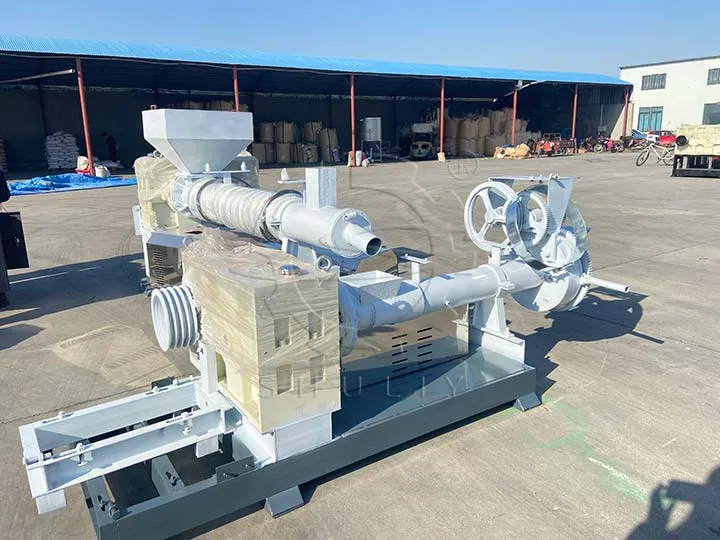
Water ring cutting
Water ring cutting refers to the extruder extruded strips of material immediately by the rotating blade cutting granules, and thrown to the water ring attached to the inner wall of the pelletizer rotating at high speed. The water flow then takes the pellets to the water separator for dehydration, drying, and then sending them to the material cooling device to cool down, that is, the finished product.
This production method is suitable for polyolefin material mixing and pelletizing.
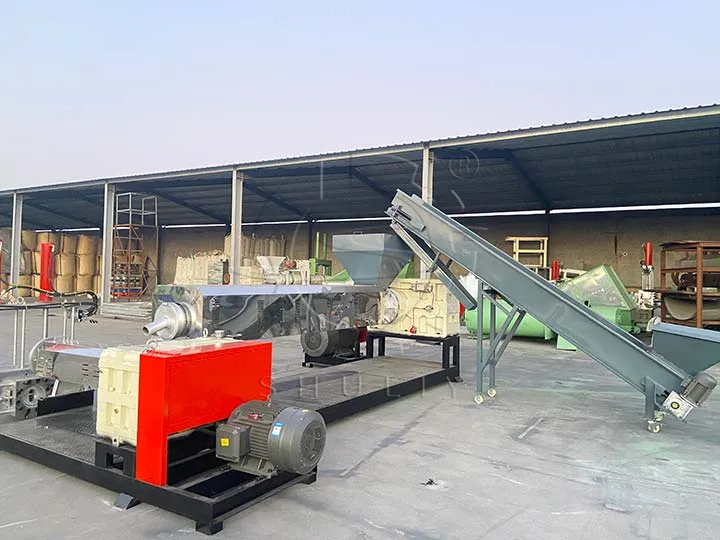
Underwater pelletizing
Underwater pelletizing refers to the PVC recycling machine extruded strip material immediately into the water cooling it down, and then cut into pellets. Then the pellets are sent to the centrifugal dryer by circulating water for dehydration and drying.
This type of pelletizing is more suitable for twin-screw waste plastic pellet making machines mixing raw materials pelletizing, for larger mass production.
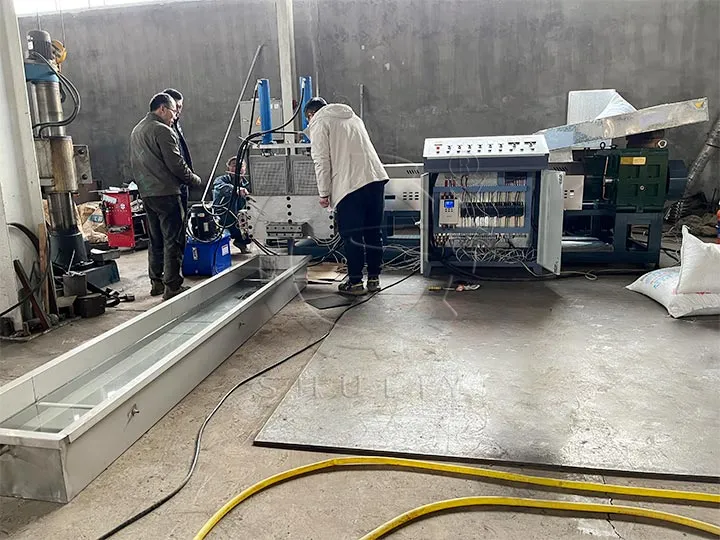
Cold cutting pellet
Cooling granule refers to the material after mixing and plasticizing by a waste plastic pellet making machine. From the HDPE plastic recycling machine granulator barrel in front of the mold into plastic flakes material. First, fall into the sink to cool down the temperature of the roll, and then use the pelletizer to cut the pellets.
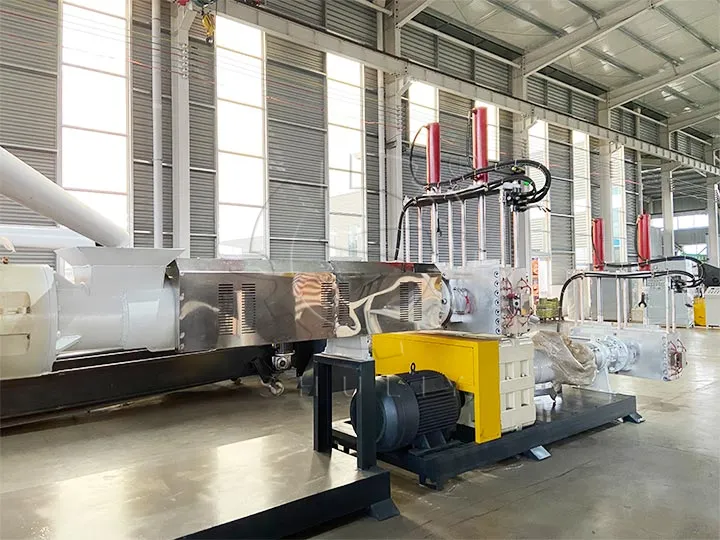
This extrusion pelletizing production method is suitable for polyethylene, polypropylene, ABS, and polyethylene terephthalate raw material mixing and pelletizing.